Life science quality leaders operating in FDA-regulated industries have a lot on their plates 2020. We recently surveyed 29 of them working inside organizations of all sizes to answer the critical questions:
- What goals are quality leaders are working to achieve?
- What challenges stand in their way?
- What are they going to do to overcome them and stay competitive?
This article offers an excerpt from our full survey report: The Life Science Quality Leadership Report & Benchmark. Be sure to download the free PDF here, where you'll find all of this information and much more.
1. Compliance & production represent the top quality goals in 2020.
90% of quality leaders we surveyed identified “maintaining compliance” among their top three challenges in 2020.
A whopping 90% of our respondents identified “maintaining compliance” among their top three challenges in the new year. “Improving manufacturing/production performance” followed at 63%, and “bringing new products to market” took the number three spot at 46%.
The overwhelming focus on compliance aligns with findings of a similar study conducted by Deloitte, which interviewed 11 major life science leaders to take a more granular look at the specific challenges life science firms are facing in the realm of compliance.
“The life sciences industry continues to face unprecedented challenges amid increasing regulatory scrutiny. Globalization, alliances and partnerships, heightened transparency expectations, increased emphasis on innovative technologies, and the ever evolving needs of existing and emerging customers are driving companies to re-examine their approach to compliance.” – DELOITTE CENTRE FOR HEALTH SOLUTIONS
The conversation around compliance flows into the second most-identified goal: improving manufacturing/product performance. Since quality teams are naturally intertwined throughout the entire production chain, their effectiveness is often a signal of broader operational and organizational health.
Issues in quality operations, whether due to chronic understaffing, skillset gaps, process problems, or any other underlying problem, inevitably increase risks and costs. High-performing quality teams keep these issues off the radar by putting a premium on preventive action.
When problems do arise, teams can more quickly identify and resolve them to avoid rippling effects that impact production and pose possible safety risks. Prior research has indicated a growing shift toward performance-oriented goals for quality operations, which by our numbers, seem to be holding in 2020.
63% of quality leaders we surveyed identified “limited headcount” as the top obstacle to reaching their goals in 2020.
Quality leaders identified “limited headcount,” “limited budget,” and “limited skillsets” as the top obstacles to achieving their goals in 2020.
Concerning budget, most quality teams also reported they anticipate holding steady at their current rate of investment or expect to receive more support over the next year.
These findings may indicate that while quality leaders are getting more of the budget they need, the challenges on the horizon will require even greater support from within, making it all the more important for quality teams to demonstrate the value of their accomplishments.
The growing role of quality teams can be seen as an opportunity to clearly show executive management both the raising stakes of quality and compliance as well as the progress made towards accomplishing a growing list of goals. Provide metrics that show the contributions your team has made and make a case for quality assurance in the context of leadership’s broader goals.
In addition to increasing investment in quality operations, the rapid rise in contracted engagements has demonstrated that leaders are not only adept at pursuing cost-effective outsourcing measures to free up internal resources, but are finding themselves more empowered to do just that. When the right balance is struck, quality leaders can redirect their focus on planning and overseeing more significant initiatives and mitigating risks proactively.
With regard to resourcing, under which we can broadly group headcount and skillset deficiencies, it appears a tightening labor market is compounding with a growing array of resourcing needs that are more particular in the skillsets and competencies they demand.
In response to resourcing challenges, which, by all indications, will only accelerate, many manufacturers are adopting innovative hiring structures and targeted partnerships with resourcing firms.
These firms can work directly with hiring managers to circumvent the traditionally slow and arduous hiring process and provide access to large benches of talent to fulfill the specific needs of the hire through either a contracted or direct hire arrangement.
At The FDA Group, we connect life science companies to the resources they need through the hiring arrangement that’s best suited to the project, role, or function whether it’s a contracted full-time engagement or direct hire. Learn more about our life science staff augmentation and recruitment services. Contact us to connect with the resources you need to accomplish quality goals in 2020 and beyond. |
3. Compliance and resourcing are the biggest upcoming challenges within the quality system.
66% of quality leaders we surveyed indicated “sufficient staffing/ resourcing” as a top quality system challenge in 2020.
The focus on compliance and resourcing in 2020 also extends directly into the quality system itself. 73% of the quality leaders we surveyed identified “ensuring compliance with relevant regulations” among their top three quality system-specific challenges.
Just as notably, the pervasive personnel problem emerged in a very close second place, with “sufficient staffing/resourcing” receiving 66%. Supplier management, system integration, and user training took the next three positions, respectively.
In considering what practical steps to take based on these findings, perhaps the best place to start in preparing your quality system for a compliant 2020 is reviewing the most recent compliance trends throughout the previous year.
For drugmakers, the most frequent known compliance issues over the last fiscal year primarily concern the basic requirements that every pharmaceutical company should have established as a matter of course. Here are the top five trending issues for drugmakers by the number of warning letters issued over the previous fiscal year, as reported by the ECA.
-
Responsibilities of the quality unit (21 CFR 211.22) – 41 Warning Letters
-
Written procedures; deviations (21 CFR 211.100) – 32 Warning Letters
-
Testing and release for distribution (21 CFR 21.165) – 29 Warning Letters
-
Production record review (21 CFR 211.192) - 27 Warning Letters
-
Testing and approval or rejection of components, drugs product containers, and closures (21 CFR 211.165) & Stability testing (21 CFR 211.166) - 22 Warning Letters
For device makers, far fewer publicly-available enforcement actions make trends far more challenging to define, however, recent data shows that most quality system issues fall in line with those that routinely get the most attention from regulators, namely:
-
CAPA (21 CFR 820.100)
-
Design controls (21 CFR 820.30)
-
Purchasing controls (21 CFR 820.50)
-
Process validation (21 CFR 820.75)
-
Complaint files (21 CFR 820.198)
While it’s no surprise that compliance tops the list of quality system challenges, resourcing as a close second appears to be an emerging point of focus, especially given how little comparative attention it garners among industry thought leaders.
Resourcing is one area where regulators have spelled out specific expectations for compliance. For drugmakers, specifically, FDA’s landmark 2006 guidance, Quality Systems Approach to Pharmaceutical Current Good Manufacturing Practice Regulations, offers a practical explanation of the roles and responsibilities within the Quality Unit. We’ve highlighted a number of the critical points for evaluating whether or not a quality function is resourced sufficiently.
The duties of the Quality Unit:
- “Ensuring that controls are implemented and completed satisfactorily during manufacturing operations”
- “Ensuring that developed procedures and specifications are appropriate and followed, including those used by a firm under contract to the manufacturer”
- “Approving or rejecting incoming materials, in-process materials, and drug products”
- “Reviewing production records and investigating any unexplained discrepancies”
Download our free report for a more detailed checklist you can use to gauge resourcing sufficiency throughout your Quality Unit.
In addition to outlining the Quality Unit’s responsibilities, FDA notes that under a quality system, “it is normally expected that the product and process development units, the manufacturing units, and the QU will remain independent.”
Regulators specifically warn against assigning a single individual to perform both production and quality functions except in “very limited circumstances.”
“In very limited circumstances, a single individual can perform both production and quality functions. That person is still accountable for implementing all the controls and reviewing the results of manufacture to ensure that product quality standards have been met. Under such circumstances, it is recommended that another qualified individual, not involved in the production operation, conduct an additional, periodic review of QU activities.”
This expectation is especially salient given the uptick in Warning Letters citing Quality Unit deficiencies in 2018 and 2019.
Many of these issues are rooted not only in establishing and documenting quality roles and responsibilities but sufficiently staffing the unit with the personnel required to adequately carry out the unit’s duties as they’ve been established and documented.
As these Warning Letters demonstrate, regulators expect firms to staff their Quality Unit to reflect the scope and complexity of the manufacturing operations under their oversight. When regulators discover that such a vital function is under-resourced (whether in terms of the number of personnel or the qualifications they carry), it’s often a signal that other deficiencies may exist due to resourcing—sparking further investigation and scrutiny.
4. Quality teams have mixed QMS priorities, but documentation, risk analysis, and CAPA stand out.
43% of quality leaders we surveyed indicated “documentation” was among the top QMS priorities in 2020.
The most varied responses came from our question regarding the quality management system. “Documentation” narrowly edged out “risk analysis” and “corrective and preventive action (CAPA, complaints, and recalls), at 43% compared to 40% for the two runners up, respectively.
While these trends have been the subject of countless articles, seminars, and workshops, a few points are important to highlight:
Documentation
- Receiving parts or products built to an out-of-date specification
- Quality events arising from lack of awareness or inadequate training
- Scrambling during gap assessments and audits to come up with a required process or specification documents
Risk Analysis
CAPA
5. Most quality teams see resourcing as a challenge in 2020 and prioritize fit, skills, knowledge, and expertise over price in potential candidates
86% of quality leaders we surveyed prioritize “right-fit skills and knowledge” when evaluating a resourcing firm.
Our survey concluded by focusing on further unpacking what turned out to be a major theme throughout the research: RA/QA resourcing.
Specifically, when asked to place their likelihood of encountering staffing/resourcing/recruiting challenges on a scale of one to ten (one being not likely at all and ten being certain), the average score landed just over six.
We also investigated the factors quality leaders prioritize when setting out to staff their team by engaging with a life science resourcing firm. While conventional wisdom suggests to many that price and/or rate is ultimately the deciding factor in a hiring decision (whether contracted or permanent placement), most quality leaders we surveyed put a higher premium on “right-fit skills and knowledge” (86%) and “industry-specific experience and expertise” (73%). “Price/rate” took the number three spot at 53%.
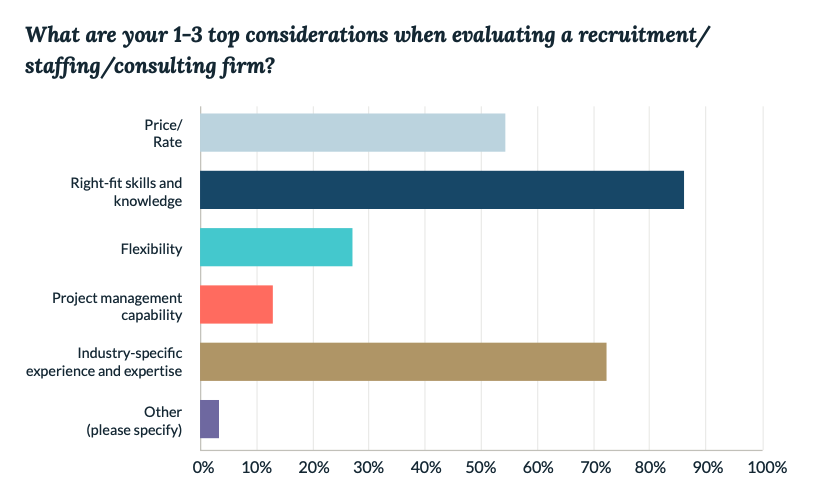
Conclusion and next steps for quality leaders
This survey revealed compliance and production performance as general priorities across quality teams, but indicated that resourcing has emerged as a large and growing problem as the labor market tightens for skilled professionals. With over half of our survey respondents anticipating quality budget increases in the year ahead, now is the time for leaders to carefully evaluate the demands of their goals for the upcoming year and assess their ability to achieve them.
If you need assistance, whether in supporting a current or upcoming project or finding a contracted or direct hire resource, The FDA Group’s large network of life science resources have extensive knowledge and experience in relevant regulations, guidance, and best practices related to quality system management throughout the regulated life science industries.
Our resources can be utilized to meet the full range of quality and compliance requirements throughout the life sciences, as well as to support staffing assignments, lead and manage related activities, bridge staffing gaps, and provide long-term or interim leadership.
Contact us to learn more about fulfilling life science resourcing needs and be sure to grab the full version of our report below. We help life science organizations secure a wide variety of resources with the perfect combination of qualifications, experience, and motivation for succeeding in challenging and demanding projects—all at a competitive rate and backed by a Total Quality Guarantee.
The Life Science Quality Leadership Report & Benchmark